6 Min Read
For decades, paper work orders have been the backbone of countless industries, serving as a tangible record of tasks and their completion. However, the digital revolution has brought about a paradigm shift.
Traditional systems are proving cumbersome and inefficient. Hence, modern businesses are increasingly adopting digital work order solutions. This shift has prompted a critical question: how do paper vs digital work order systems compare?
This guide will share a definitive answer to this ongoing debate, examining the strengths and weaknesses of paper vs digital work orders, as well as their impact on efficiency, data accessibility, and workflow management. Let’s dig in!
What Do You Mean By Work Order?
When it comes to organizational tasks and asset management projects, a work order stands as a fundamental document. It serves as a formal authorization and detailed record for executing maintenance, repair, or operational activities. This essential document captures all the critical information about a specific job. Ultimately ensuring clear communication and streamlined workflows.
Typically, a work order form encompasses elements such as:
- Request Details:A comprehensive description of the required task or service.
- Requester Identification:The individual or department initiating the work order.
- Location:Precise designation of where the work needs to be performed.
- Priority Level:The urgency associated with the work order influences its placement within the overall workload.
- Authorization:Approval by a designated authority to proceed with the work.
- Resource Allocation:Specification of required personnel, materials, or equipment.
- Expected Outcome:A clear definition of the desired result upon completion.
PRO TIP:
Integrate The NonStop Suite into your asset management strategy and take your work order system into the future. By functioning as a central hub for job-related information, The NonStop Suite promotes efficient task management and fosters accountability. Hence, your organization can effectively manage its maintenance operations, prioritize tasks, and track the progress of essential work.
Smarter Asset Tracking With NFC Tags
Learn more about how NonStop Suite's NFC Asset Tracking Solution can help your Enterprise streamline operations to new heights.
Get A Free Product Tour
What are Paper Work Orders?
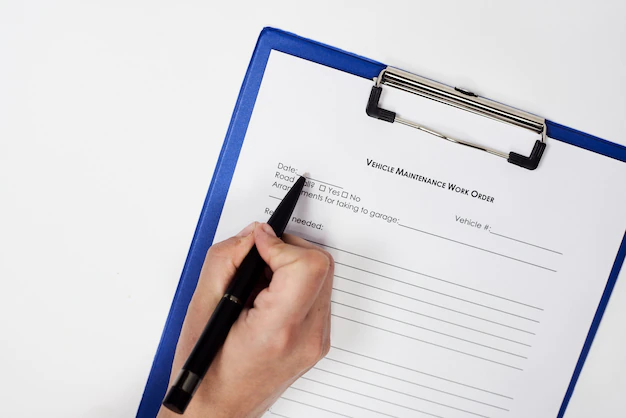
Paper work orders are physical documents that serve as formal directives, guiding workers on tasks and providing a record of completed work. These paper-based forms typically outline the specific work required, its location, necessary materials or tools, and information about the requester and worker assigned to the job. Despite the increasing prevalence of digital systems, paper work orders remain common in manufacturing, construction, maintenance, and utilities. They serve as tangible records of tasks or maintenance requests within an organization.
Pros of Paper Work Orders
- Simplicity:A paper work order is familiar and easy to understand for many users, requiring minimal training.
- Accessibility:A physical copy of the work order is always readily available, without dependence on internet connectivity or specific software.
- Tangible Record:Paper work orders provide a physical record that can be easily archived and referenced later.
Cons of Paper Work Orders
- Inefficiency:Paper-based systems can be slow and cumbersome when managing and tracking work orders.
- Data Silos:Information on paper work orders is isolated and not easily shared or integrated with other systems.
- Prone to Errors:Manual data entry on paper forms can be susceptible to errors and inconsistencies.
- Loss or Damage:Physical copies of work orders can be misplaced, damaged, or lost permanently.
- Limited Visibility:Real-time tracking of work progress and resource allocation can be difficult with paper systems.
What are Digital Work Orders?
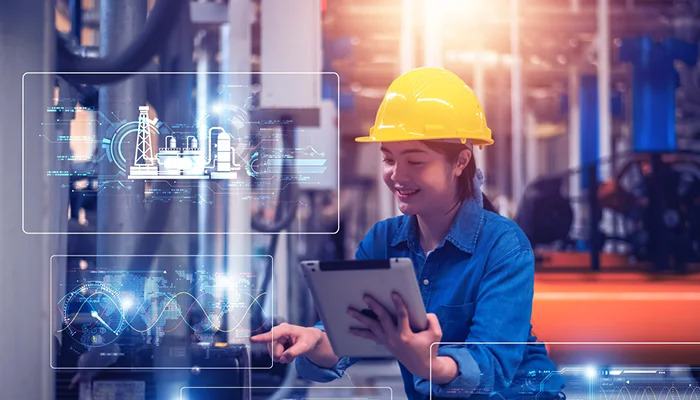
In this epoch of digitalization, traditional paper-based work orders are steadily being replaced by their electronic counterparts. Digital work orders are essentially electronic records that detail tasks, resources, and procedures required to complete a specific job. Deployed on cloud-powered solutions, these records are typically created, managed, and accessed using specialized software or applications. Consequently, they offer a more streamlined and efficient approach to workflow management.
Pros of Digital Work Orders
- Enhanced Efficiency and Accuracy:Digital work order management systems streamline workflows by automating tasks and eliminating manual data entry. This reduces the risk of errors and allows for faster job completion.
- Improved Accessibility and Visibility:Digital records can be accessed from anywhere with an internet connection, providing all stakeholders real-time visibility into work progress.
- Reduced Paper work and Environmental Impact:Digital work orders contribute to a more sustainable work environment by eliminating the need for paper forms.
- Enhanced Communication and Collaboration:Digital platforms facilitate communication and collaboration between teams involved in a project so they are always immediately informed.
- Data-Driven Insights and Decision Making:Digital work order systems provide valuable data that can be analyzed to identify trends, optimize processes, and make informed decisions.
- Reduced Costs:Eliminating paper, filing systems, and physical copies translates to significant money savings.
Cons of Digital Work Orders
- Initial Investment Costs:Implementing a digital work order system may require an upfront investment in software and potentially new hardware.
- Technical Dependence:Reliance on technology creates a vulnerability in case of internet outages or software malfunctions.
- Potential Learning Curve:A shift from traditional paper systems may require some initial training for users to adapt to the new platform.
- Potential Security Concerns:Digital systems require adequate cybersecurity measures to protect sensitive work order data.
What is The Difference Between Paper and Digital Work Orders?
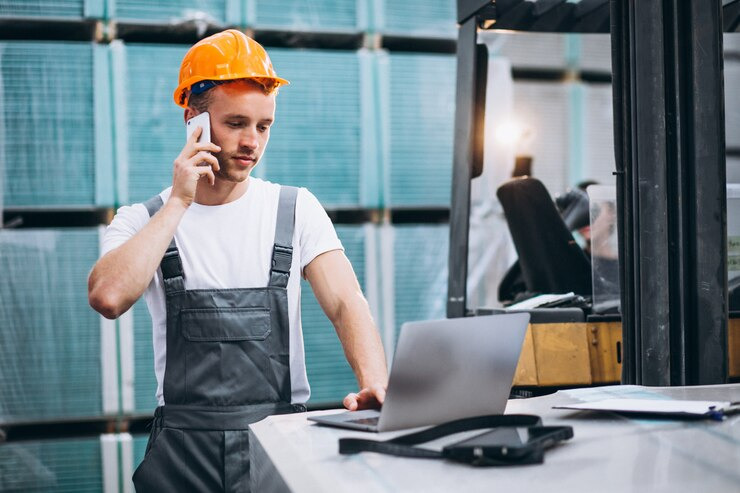
The fundamental difference between paper and digital work orders lies in their format and functionality. Here’s a comprehensive table outlining the main differences between paper and digital work orders:
Feature | Paper Work Orders | Digital Work Orders | Winner |
Accessibility | Physical documents, accessible in person | Accessed digitally, potentially from anywhere | Digital Work Orders |
Storage | Physical filing systems | Electronic databases or cloud storage | Digital Work Orders |
Data Entry | Manual entry, potentially prone to errors | Automated entry, reducing errors | Digital Work Orders |
Mobility | Limited mobility may require physical transfer | Highly mobile, accessible via devices | Digital Work Orders |
Retrieval | May require manual search | Searchable electronically, faster retrieval | Digital Work Orders |
Updates | Manual updates, potentially time-consuming | Real-time updates, immediate visibility | Digital Work Orders |
Collaboration | Limited collaboration, often sequential | Allows for real-time collaboration, comments, etc. | Digital Work Orders |
Environmental Impact | Consumes paper, ink, potentially wasteful | Environmentally friendly, reduces paper usage | Digital Work Orders |
Integration | Limited integration with other systems | Can integrate with other digital systems easily | Digital Work Orders |
Cost | Initial setup costs for paper and printing | Potential subscription or software licensing fees | Digital Work Orders |
Security | Physical security measures required | Digital encryption, access controls, and backups | Digital Work Orders |
Scalability | Limited scalability due to physical constraints | Highly scalable, can accommodate growth | Digital Work Orders |
PRO TIP
In nearly all aspects, digital work order systems emerge as the winner. Amplify your organization’s asset and data management strategy by leveraging the transformative power of NonStop Suite. With its advanced features and seamless integration, The NonStop Suite empowers businesses to streamline processes, enhance productivity, and optimize resource utilization.
What are the Benefits of Using a CMMS to Create Digital Work Orders?

In today’s digital age, many businesses are rethinking traditional paper-based systems to streamline processes and improve efficiency. Ditching paper and embracing digital work orders is a decisive step towards achieving these goals.
Work order based on a Computerized Maintenance Management System (CMMS) not only enhances workflow but also delivers many benefits that directly impact your bottom line. Detailed below are the five key benefits of digital work orders that will make your organization want to shift to paperless:
Paper vs. Digital Work Orders: Efficient Workflows
Digital work orders eliminate the time-consuming tasks associated with paper-based systems. Maintenance technicians can access work orders and real-time updates on mobile devices, reducing confusion and delays. Additionally, digital workflows automate processes such as work order routing and status updates. This efficiency frees up valuable time for technicians to focus on completing jobs.
Better Resource Management
Digital work orders provide a centralized platform for managing resources like equipment and personnel. With all work order information readily available, businesses can optimize resource allocation, ensuring the right people and tools are assigned to the right jobs. This efficacy translates to faster completion times and reduced costs.
Facilitation of Continuous Improvement
Digital work orders enable businesses to gather valuable data on work order completion times, resource usage, and potential problem areas. Analyzing this data helps identify areas for improvement. As a result, businesses are able to refine their processes for greater efficiency and effectiveness.
Simplified Reporting and Data Analysis
Gone are the days of sifting through mountains of paper to generate reports. Digital work orders provide instant access to historical data and allow for easy generation of comprehensive reports. This data accessibility empowers businesses to gain deeper insights into their operations, identify trends, and make data-driven decisions. Additionally, digital reports are readily available, saving time and resources compared to manually compiling information from paper records.
Cost Savings Across the Board
Paper, printing, storage, and physical distribution of work orders all contribute to operational expenses. Digital systems eliminate these costs and offer additional savings through improved resource allocation and reduced administrative overhead. Faster completion times translate to quicker project turnaround, leading to potential revenue gains.
PRO TIP
Bid farewell to traditional paper-based work orders and welcome the operational excellence of digital work orders with The NonStop Suite. By consolidating the maintenance management workflows into one intuitive platform, your organization can unlock a new level of efficiency and transparency. With real-time insights and seamless communication, your organization can stay ahead of maintenance needs, optimize resources, and keep your facilities running smoothly.
Conclusion: Go Paperless With The NonStop Suite!
The transition from paper to digital work orders offers streamlined workflows, data-driven decision-making, and a commitment to sustainability. While the change might seem daunting, the process can be surprisingly smooth with the right tools.
The NonStop Group empowers businesses to embrace digital work orders effortlessly with The Nonstop Suite — a full suite for on-the-go asset management. Its intuitive interface and user-friendly features make it easy for technicians of all tech levels to adapt. However, the pivotal transformation lies in Nonstop Suite’s Dynamic eForms, NFC asset tagging system, and GxP & ISO Specific NC-CAPA Capabilities.
The Nonstop Suite enables businesses to create custom digital work orders tailored to their needs. From making work orders and capturing essential job details to automating approval workflows and eliminating the need for manual data entry, this digital suite streamlines your organization’s operations. Consequently, your organization can move towards greater efficiency and profitability.
Should you want to unlock the power of digital work orders, consult The NonStop Group today. Book a FREE personalized product tour and experience a truly seamless transition to a paperless future.